Immark AG, входящая в группу Thommen, является пионером и лидером рынка в области переработки и утилизации электронных отходов в Швейцарии. Уровень переработки достигает 95 %, что значительно превышает требования Европейской директивы по отходам электрического и электронного оборудования (WEEE). ).
12.12.2023 Подписывайтесь на наш канал в Telegram
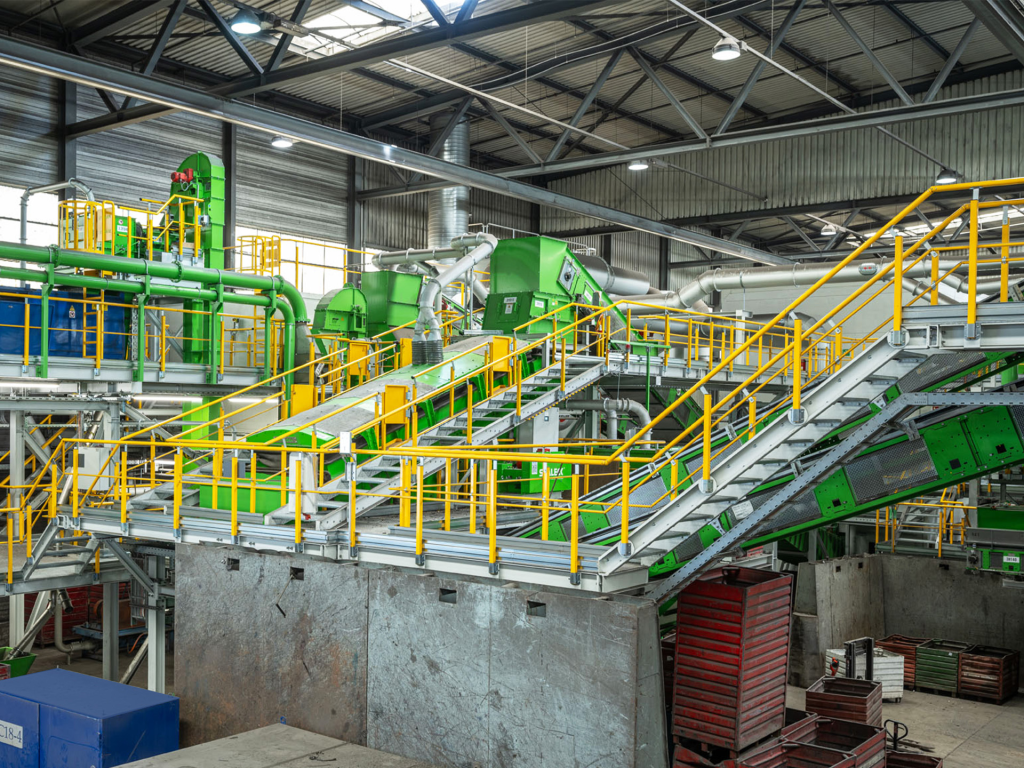
Компания выбрала компанию Stadler для проектирования и установки новой сортировочной установки взамен существующей в Регенсдорфе.
«Это крупнейший завод по переработке электронных отходов в Швейцарии, и он должен обеспечивать высокую производительность и способность перерабатывать получаемые нами объемы», — говорит Патрик Волленманн, руководитель проекта в Immark. «Мы ожидаем, что с этим новым заводом мы заложим основу для успешного будущего с точки зрения оперативного управления».
Новое предприятие отличается инновационным дизайном и новейшими технологиями и, по сути, является первым заводом по сортировке электронного мусора, использующим баллистический сепаратор. Завод работает в две смены с производительностью до 12 тонн в час, что соответствует требованиям Immark по большей производительности и большей чистоте продукции. Это также оптимизирует восстановление печатных плат.
«Для нас решающее значение имели убедительные технологии Stadler в области ленточных конвейеров и баллистических сепараторов, а также их близость к Цюриху. Мы также очень ценим работу компетентных менеджеров проектов, быструю и конструктивную реализацию и подход, ориентированный на решение», — говорит Патрик Волленманн.
«Баллистический сепаратор Stadler STT5000 предварительно сортирует материал на три различные фракции. Он разделяет материал на мелкие детали, плоские пластмассы и кабели, а также на материалы кубической формы, такие как электронные двигатели», — объясняет Ян Долленмайер, совместный руководитель проекта Stadler.
На новый сортировочный завод поступают материалы, относящиеся к группам директив WEEE 1–3 (Крупная – малая бытовая техника и ИТ-оборудование) и 4 (Бытовое оборудование), которые обрабатываются в нескольких модулях обработки. Модули расположены в ряд, но также оснащены отдельными питателями для независимого использования, что повышает эксплуатационную готовность всей установки.
Гибкая модульная конструкция завода позволяет настраивать машины на протяжении всего процесса для обеспечения стабильно высокого качества цветной, черной, полихлорированной, нержавеющей стали и пластиковой фракции.
В первом модуле процесса поступающий материал сортируется вручную для удаления токсинов и опасных компонентов, а также ценных материалов, таких как кабели, печатные платы и металлы.
После удаления опасных компонентов материал измельчается в различных измельчителях, чтобы можно было отсортировать как оставшиеся опасные компоненты, такие как батареи или конденсаторы, так и различные пригодные для вторичной переработки материалы, такие как железо, цветные металлы и пластик. При выборе измельчительных агрегатов учитывались не только требуемая производительность, но и минимально возможный износ и простота обслуживания.
Вторсырье сортируется после сортировки с использованием современной магнитной технологии, вихретоковой сепарации и сенсорной технологии сортировки. Железные фракции повторно сортируются в сортировочной камере для обеспечения качества и повышения степени чистоты.
Мелкая фракция также проходит различные этапы сортировки для отделения пластика от соединений металлов, которые затем измельчаются для отделения различных металлических гранул.
Большое внимание на заводе уделялось пожарной безопасности. За измельчительными установками установлены автоматизированные системы обнаружения и тушения пожара. Обнаруженный источник пожара автоматически выгружается из производственного процесса в стальной бункер через систему люков, где персонал может потушить пожар и зафиксировать источник огня. Высокий износ отходов, перерабатываемых на новом заводе, потребовал особых конструктивных особенностей, таких как износостойкие пластины из нержавеющей стали для усиления бункеров и лент с огнезащитными свойствами и защитой от порезов.
Завод также был спроектирован так, чтобы максимально упростить техническое обслуживание. Доступ ко всем ключевым точкам и двигателям осуществляется через платформы обслуживания или лестницы.
Проектирование и монтаж нового завода поставили перед собой задачи, которые команды Stadler и Immark успешно решили благодаря тесному сотрудничеству.
«Помимо установки новой системы, продолжала работать старая система. Это означало, что новый завод пришлось строить в несколько этапов, а старый завод нужно было одновременно демонтировать. Кроме того, доступная площадь на строительной площадке была очень ограничена», — говорит Патрик Волленманн.
Модульная конструкция нового завода стала ключевым элементом успешного завершения проекта и высокой скорости сборки: «Модульная конструкция отдельных агрегатов ограничила время сборки до очень короткого периода. Любые проблемы, возникавшие во время сборки, быстро выявлялись и решались благодаря гибкости сотрудников Stadler», — добавляет Патрик Волленманн.
«Это был крупный проект по утилизации отходов электрооборудования, в котором было установлено много нового оборудования и задействовано множество поставщиков. У нас было много новых интерфейсов. В целом, в сотрудничестве с командой Immark нам все удалось очень хорошо», — заключает Филипп Фрехен, совместный руководитель проекта Stadler.