Достижения в области электролиза могут превратить отходы производства аккумуляторов электромобилей в ценный товар. Уилл Гирлинг
Одна из самых ярких ироний электрификации заключается в том, что продукция, разработанная с расчетом на большую экологичность, в настоящее время имеет относительно неустойчивые цепочки поставок. Производство аккумуляторов для электромобилей (ЭМ) особенно сопряжено с проблемами ESG . Например, для производства всего одной тонны лития (достаточно примерно для 100 ЭМ) требуется два миллиона тонн воды, а методы извлечения часто оказываются вредными для пострадавших районов.
Цифровые паспорта аккумуляторов — одна из идей по улучшению экологичности этих важных компонентов. С февраля 2027 года все транспортные средства, продаваемые в ЕС, должны включать QR-код с такой информацией, как состав материалов и встроенный углеродный след. Со временем OEM-производители также должны будут продемонстрировать соблюдение предварительно установленных норм извлечения металла и спецификаций переработанного содержимого.
Поскольку эти данные формируют решения потребителей о покупке и оказывают давление на мировых автопроизводителей, требуя повышения их устойчивости, миссия по декарбонизации аккумуляторов электромобилей неизбежно повлечет за собой переоценку всей цепочки создания стоимости. От критической обработки минералов до производства катодов каждый шаг должен быть пересмотрен. Но есть ли общая проблема во всем?
Осознание потенциала
В 2020 году два выпускника Калифорнийского университета в Беркли — Лукас Хакл и Билен Акузум — отправились в поездку, чтобы посетить компании по всей цепочке поставок аккумуляторов для электромобилей в Калифорнии и Неваде. «Мы посетили горнодобывающие предприятия, предприятия по переработке аккумуляторов, производителей катодных активных материалов и многое другое», — рассказал Акузум Automotive World . «Мы держали уши открытыми, чтобы понять, откуда на самом деле берутся проблемы». К их удивлению, независимо от места поставщика в цепочке создания стоимости, один и тот же отход упоминался неоднократно.
Сульфат натрия — побочный продукт, получаемый при использовании серной кислоты и каустической соды во время очистки критических металлов для производства обычных катодов, включая никель-марганец-кобальт. Он также создается во время переработки аккумуляторов — модель EverBatt Аргоннской национальной лаборатории оценивает, что на 1000 кг переработанных материалов для аккумуляторов производится 800 кг. Сульфат натрия имеет ограниченное коммерческое применение, но рост производства аккумуляторов для электромобилей означает, что ответственная утилизация больших объемов становится затруднительной.
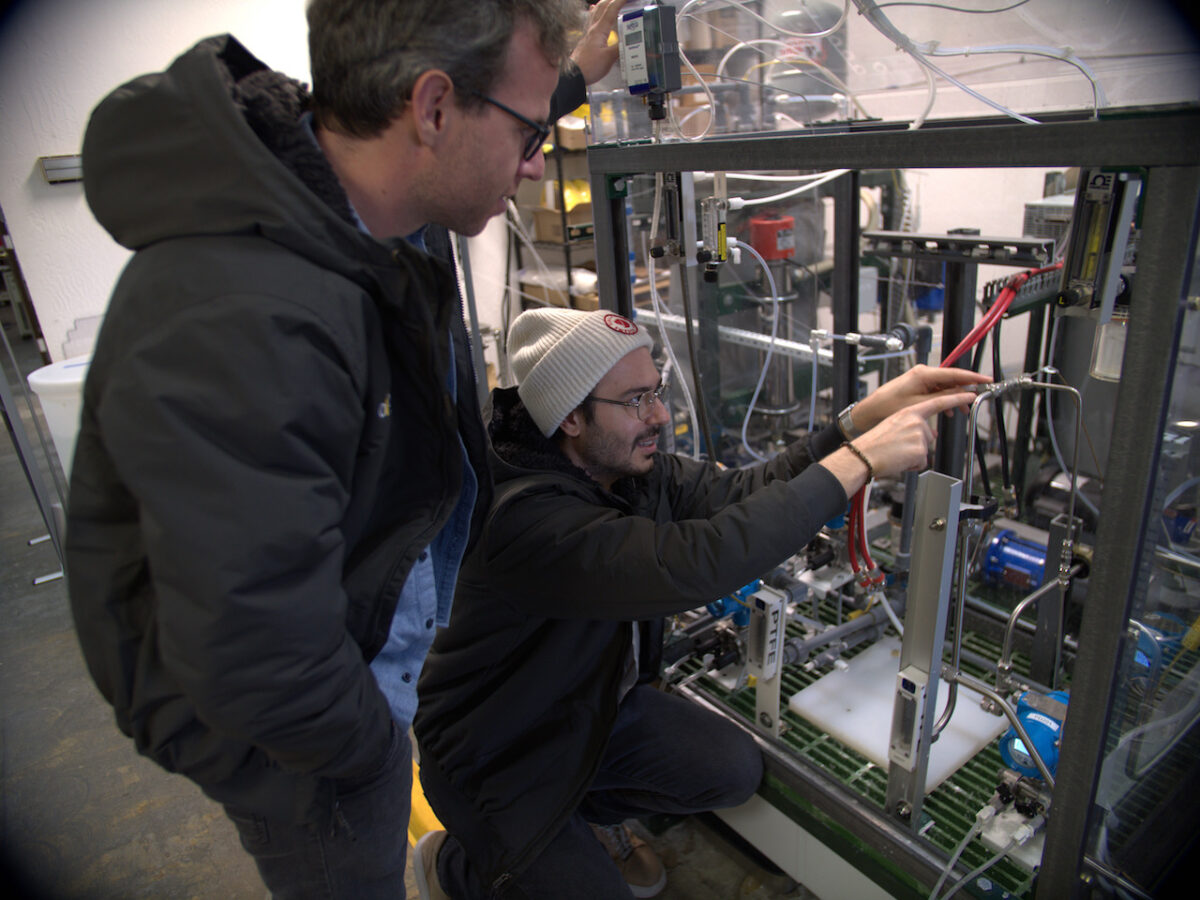
Потенциал более чистой электрифицированной химической обработки, добавляет Хакл, имеет «огромный» потенциал. «Существует множество различных подходов к этому в автомобильной промышленности — от зеленого водорода до улавливания углерода, — но мы хотели выбрать область, которая решает реальные проблемы поставщиков сегодня». Таким образом, в 2021 году Хакл и Акузум совместно основали Aepnus Technology — в качестве генерального директора и главного технологического директора соответственно — для сокращения выбросов химикатов в цепочке поставок аккумуляторов за счет сверхэффективного электролиза.
Закрытие цикла
Решение Aepnus Technology заключалось в разработке нового электролизера — стопки металлических электродов, разделенных мембранами и питаемых водным сырьем, которое затем превращается в желаемые химические продукты с помощью применения электричества. «Вот как мы можем взять сульфат натрия и преобразовать его обратно в два рабочих реагента для аккумуляторной промышленности: серную кислоту и каустическую соду», — объясняет Хакл. По сути, компания берет то, что раньше было отходами, направляемыми на свалку, и снова вводит его составные части в цепочку поставок.
Химикаты, полученные с помощью этого метода, продолжает он, столь же жизнеспособны, как и эквиваленты из первичного источника. «Традиционно эти молекулы доставляются на грузовиках или поездах в чрезмерно концентрированной форме, которую затем необходимо разбавить в пункте назначения для фактического использования». Вместо того, чтобы хранить определенное количество воды для этой цели, клиенты смогут держать электролизер Aepnus Technology на месте. Важно то, что это означает, что они могут снизить логистические расходы и производить более дешевые — в зависимости от цены на электроэнергию — химикаты для обработки аккумуляторов в точных требуемых концентрациях.
«Это может ускорить время выхода аккумуляторов на рынок во многих отношениях», — говорит Хакл. «Поскольку больше нет потока отходов, компаниям не нужно разрешение на его смягчение; цикл замкнулся». Aepnus Technology ввела в эксплуатацию свою пилотную систему в начале 2024 года, и неуказанный заказчик уже присоединился к ней. Akuzum заявляет, что первоначальный объем производства будет небольшим — две тонны в год, капля в море, когда один завод по производству аккумуляторов производит «десятки тысяч тонн» сульфата натрия. «Как и в случае с НИОКР аккумуляторов, много времени и денег уйдет на раннюю коммерческую демонстрацию технологии. После этого масштабирование не будет такой уж сложной задачей».
Недостающая часть головоломки
В своем Национальном плане по литиевым батареям 2021 года Министерство энергетики США подчеркнуло уязвимость внутренних цепочек поставок к чрезмерной зависимости от иностранного импорта, что также является распространенной проблемой в Европе. Электролизер Aepnus Technology открывает перспективы оншоринга и повышения устойчивости важных химических веществ для обработки материалов для батарей. На момент написания статьи Akuzum заявляет, что компания находится на 10% пути к своей конечной цели. В июне 2024 года компания получила 8 млн долларов США в виде начального финансирования под руководством Clean Energy Ventures, что, как она надеется, приведет к значительному прогрессу в создании коммерчески жизнеспособного реактора в течение следующих двух лет.
Это недостающий элемент головоломки для перехода на чистую энергию.
«Электрохимия — ключ к декарбонизации отрасли, которую в противном случае очень трудно улучшить», — подчеркивает Хакл. В сочетании с растущими глобальными инвестициями в возобновляемую энергетику он предвидит будущее, в котором более дешевая и экологичная электроэнергия будет сочетаться с производством электромобилей на каждом уровне, образуя эффективный цикл, исключающий отходы. «Серная кислота и каустическая сода являются одними из наиболее широко потребляемых промышленных химикатов в мире. Существует море клиентов, и, устанавливая партнерские отношения с производителями на раннем этапе, мы надеемся включить наш электролизер в их новые, готовые к электромобилям объекты».
Хотя он не может назвать конкретные компании, Акузум утверждает, что OEM-производители и несколько игроков в цепочке создания стоимости аккумуляторов уже взаимодействуют с Aepnus Technology на этой ранней стадии. «Никто не хочет говорить о том, сколько отходов связано с производством аккумуляторов для электромобилей, но мы хотим показать, что есть решение», — заключает он. «Рыночный спрос, который мы испытываем, показывает, что это недостающий элемент головоломки для перехода на чистую энергию».